
Recykling odpadów poprodukcyjnych ze stopów aluminium w oparciu o technologię odlewania ciągłego
Projekt nr TECHMATSTRATEG1/349264/18/NCBR/2018
Wartość projektu: 5 171 875,00 PLN
Opis projektu:
Konsorcjum w składzie: Instytut Odlewnictwa w Krakowie (Lider), Politechnika Rzeszowska, Akademia Górniczo-Hutnicza w Krakowie, firmy FAM-Technika Odlewnicza Sp. z o.o. w Chełmnie i ION GALENICA w Wysokiej Głogowskiej na podstawie Umowy o dofinansowanie z dnia 29.08.2018 r., nr TECHMATSTRATEG1/349264/18/NCBR/2018 w ramach strategiczny programu badań naukowych i prac rozwojowych „Nowoczesne technologie materiałowe” TECHMATSTRATEG, realizuje projekt pt. ,,Recykling odpadów poprodukcyjnych ze stopów aluminium w oparciu o technologię odlewania ciągłego”.
Perspektywy rozwoju stopów aluminium zależą obecnie od wprowadzania do ich wytwarzania i przetwarzania wysoko zaawansowanych technologii spełniających wymagania zarówno technologiczne, jak i ekonomiczne. Duże zainteresowanie stopami aluminium wykazuje wciąż przemysł motoryzacyjny, budowlany, morski, lotniczy, kolejowy i opakowań. Aluminium charakteryzuje się zdolnością do wielokrotnego recyklingu. Ważne dla ochrony środowiska jest pozyskiwanie aluminium i jego stopów ze złomu. Aluminium może być wielokrotnie poddawane recyklingowi bez obniżenia jego jakości i właściwości oraz bez zmian w mikrostrukturze metalu. Ponowne wytworzenie aluminium ze złomu wymaga niewiele energii: w procesie recyklingu aluminium jest potrzebne tylko około 5 % energii jaka jest konieczna do wytworzenia metalu pierwotnego z boksytów. Ze względu na dużą dostępność złomu – również w postaci wiórów, ze stopów aluminium grupy 2xxx (stop 2007 i 2017A) i 6xxx (6061) oraz ich bardzo dobre właściwości wytrzymałościowe w porównaniu do innych grup stopów aluminium stopy te stanowią bardzo atrakcyjny materiał konstrukcyjny. Głównym celem projektu jest opracowanie technologii i uruchomienie produkcji wyrobów wytwarzanych ze stopów aluminium w gat. EN AW-2007 (AlCu4PbMg) oraz EN AW-2017A (AlCu4MgSi(A)). Opracowanie nowej technologii zostanie oparte o technologię odlewania ciągłego oraz zastosowaniem powłok ochronnych PVD/CVD na krystalizatorze. Zadaniem zespołu badawczego Laboratorium Badań Materiałów dla Przemysłu Lotniczego i Katedry Nauki o Materiałach Politechniki Rzeszowskiej pod kierownictwem dr. inż. Jacka Nawrockiego, jest opracowanie technologii wytwarzania powłok na krystalizatorze, symulacje numeryczne składu fazowego stopów oraz procesu odlewania, również dobór właściwych parametrów obróbki cieplnej odlanych elementów.
Projekt jest współfinansowany ze środków Narodowego Centrum Badań i Rozwoju w wysokości 3 985 045,00 PLN.
Całkowity koszt realizacji projektu w okresie 2018 - 2020: 5 171 875,00 PLN
https://www.ncbr.gov.pl/programy/programy-strategiczne/nowoczesne-technologie-materialowe-techmatstrateg/techmatstrateg-i-konkurs/
Optymalizacja kinetyki procesu utleniania poprzez obróbkę powierzchni - strategia dla wytwarzania nowych materiałów
Projekt nr 2015/19/P/ST8/03995/2
Wartość projektu: 875 464,00 PLN
Okres realizacji: 01.03.2017 - 28.02.2019 r.
Kierownik projektu: dr inż. Wojciech Nowak, Tel. +48 17 743 2375, email: wjnowak@prz.edu.pl
Opis projektu:
Celem projektu jest określenie wpływu sposobu obróbki powierzchni na kinetykę reakcji oraz rodzaj uformowanej zgorzeliny dla stopów metali pracujących w wysokiej temperaturze w obecności agresywnych atmosfer utleniających.
Dzięki analizie wyników projektu będzie można uzyskać zarówno jakościową oraz ilościową charakterystykę podstawowych procesów przebiegających w materiałach podczas pracy w wysokich temperaturach i agresywnych środowiskach utleniających. Za pomocą uzyskanych wartości stałych kinetyki reakcji stopy metali zostaną sklasyfikowane i uszeregowane pod względem odporności na korozję wysokotemperaturową. Określenie wpływu rodzaju obróbki powierzchni na kinetykę reakcji pozwoli na zoptymalizowanie procesu wytwarzania materiału do konkretnych zastosowań. Model matematyczny wpływu stopnia obróbki powierzchni materiału na kinetykę reakcji będzie narzędziem za pomocą którego możliwe będzie prognozowanie czasu życia materiału.
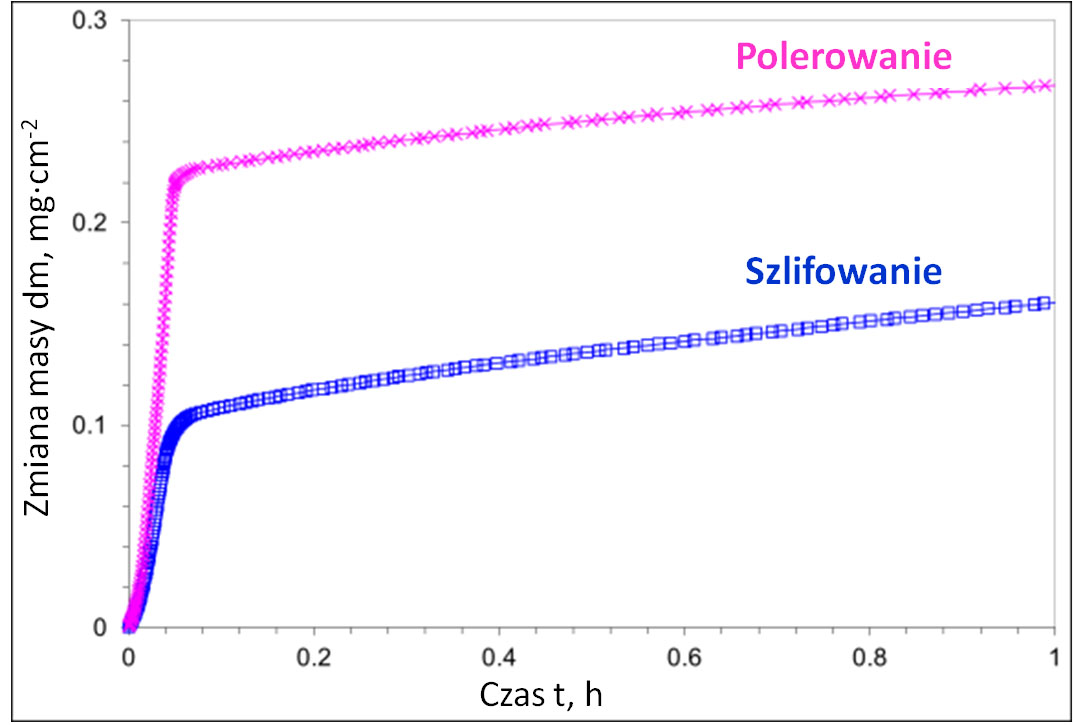
Wykres zmiany masy w czasie próby utleniania w 950°C w powietrzu dla szlifowanej i polerowanej próbki nadstopu niklu CMSX-4
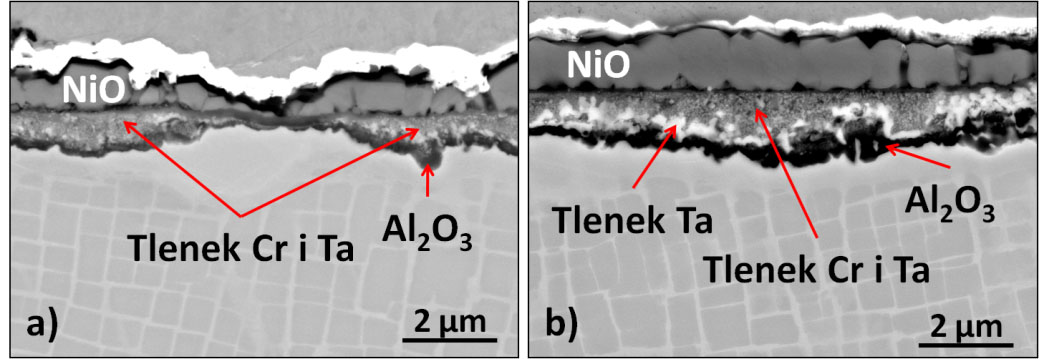
Mikrostruktura warstw tlenkowych utworzonych na szlifowanej (a) i polerowanej (b) próbce nadstopu niklu CMSX-4 w czasie próby utleniania w 950°C w powietrzu
Opracowanie technologii i wspomagania komputerowego hartowania indukcyjnego konturowego elementów stalowych o złożonych kształtach
Program Badań Stosowanych Nr: PBS2/A5/41/2014
Wartość projektu: 3 301 800,00 PLN
Wartość dofinansowania: 3 301 800,00 PLN
Okres realizacji: 01.02.2014 - 31.01.2017 r.
Opis projektu:
Projekt badań stosowanych obejmuje przeprowadzenie badań przemysłowych hartowania indukcyjnego elementów stalowych o różnych kształtach, w tym także kół zębatych. Część tych badań była przeprowadzona metodą dwu-częstotliwościową ukierunkowaną na przyszłe zastosowanie tej technologii w zaawansowanych dziedzinach gospodarki, w tym zwłaszcza w przemyśle lotniczym. Zakres zadań obejmował budowę uniwersalnego stanowiska doświadczalnego do badań przemysłowych, wybór gatunków stali do badań, identyfikację właściwości materiałowych i parametrów krytycznych dla wybranych gatunków stali, symulację komputerową oraz opracowanie programu użytkowego do projektowania urządzeń, obszerną część doświadczalną oraz ocenę jakości drogą badań metalograficznych i nieniszczących. Efektami końcowymi są między innymi: wytyczne do przygotowania normy hartowania indukcyjnego konturowego kół zębatych, opracowanie kart technologicznych, oferta technologiczna oraz ramowy plan wdrożenia.
Kierownik projektu: dr hab. inż. Grażyna Mrówka - Nowotnik, Tel. +48 17 865 36 46, email: mrowka@prz.edu.pl
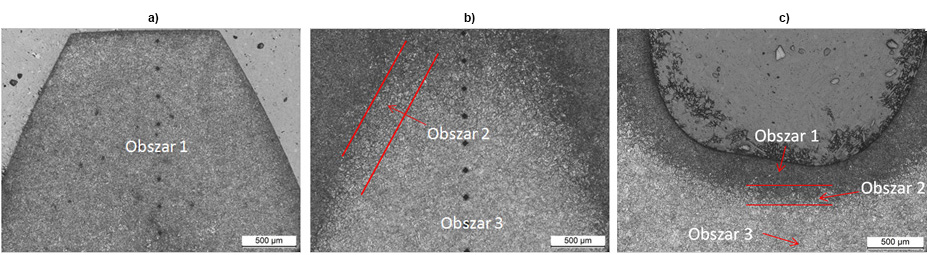
Mikrostruktura zahartowanego koła w: a, b) zębie i c) wrębie z zaznaczonymi obszarami 1-3
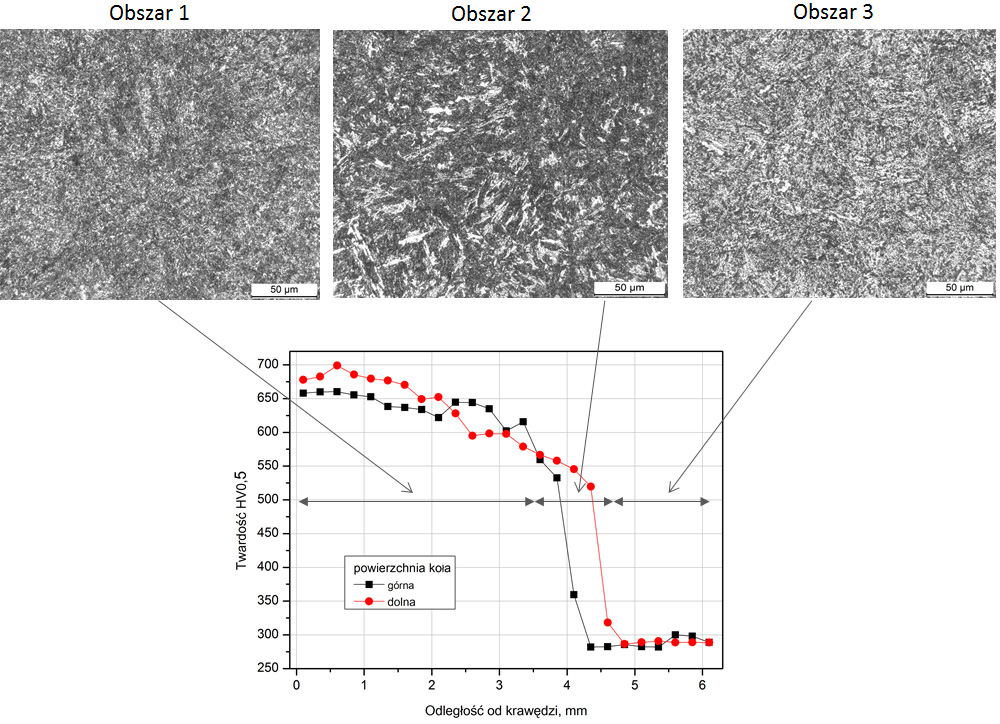
Zmiana mikrostruktury i twardości zahartowanego koła w zaznaczonych obszarach
Zastosowanie nowych metod wytwarzania powłok żaroodpornych dla wybranych elementów części gorącej silnika turbinowego w celu zwiększenia jego sprawności
Program Badań Stosowanych Nr: PBS1/A5/10/2012
Wartość projektu: 4 700 000,00 PLN
Wartość dofinansowania: 4 560 000,00 PLN
Okres realizacji: 01.12.2012 - 31.05.2015 r.
Opis projektu:
Główny cel projektu to praktyczne zastosowanie najbardziej zaawansowanych metod wytwarzania warstw żaroodpornych i powłokowych barier cieplnych na elementach silnika lotniczego umożliwiających zwiększenie jego sprawności oraz trwałości. Realizacja projektu umożliwiła dokonać praktycznej weryfikacji opracowanych parametrów wytwarzania nowych rodzajów powłok z wymaganiami procesów produkcyjnych części stosowanych przez największych światowych wytwórców silników lotniczych. W ramach projektu stosowano najbardziej zaawansowane technologie wdrożone lub będące na etapie wdrożenia stosowane w praktyce przemysłowej przez światowych wytwórców m.in. Rolls Royce, GE, P&W. W wyniku zrealizowanych prac badawczych opracowano nowe metody wytwarzania powłokowych barier cieplnych możliwych do zastosowania w silniku turbinowym charakteryzującym się mniejszym zużyciem paliwa oraz większą trwałością. Może to zapewnić ograniczenie emisji zanieczyszczeń poprzez zwiększenie temperatury na turbinie i poprawy efektywności spalania. Przyczyni się także do zwiększenia trwałości elementów silnika przez co ograniczone zostaną koszty jego eksploatacji.
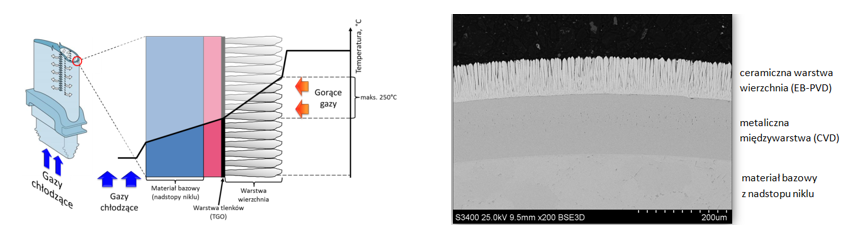
Charakterystyka pracy powłokowej bariery cieplnej na łopatce turbiny silnika lotniczego, b) mikrostruktura powłokowej bariera cieplnej z metaliczną międzywarstwą i ceramiczną warstwą wierzchnią o strukturze kolumnowej
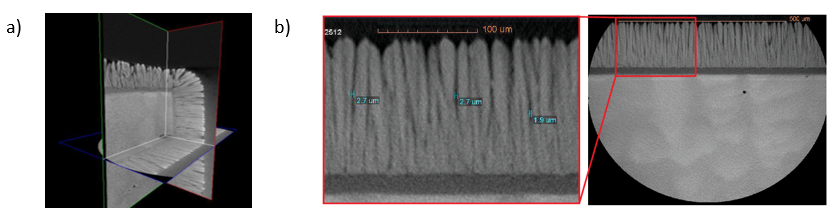
Trójwymiarowym obraz mikrostruktury powłoki TBC wytworzonej metodą EB-PVD
Kierownik projektu: dr inż. Andrzej Nowotnik, Tel. +48 17 865 11 21, email: nowotnik@prz.edu.pl
Opracowanie warunków procesu wytwarzania warstw żaroodpornych na łopatkach turbiny z nadstopu niklu z zastosowaniem fenomenologicznych modeli dyfuzji i termodynamiki procesów nieodwracalnych
Projekt rozwojowy nr N R15 0121 10
Opis projektu:
Celem projektu jest opracowanie modelu, oprogramowania wspomagającego oraz podstaw technologii wytwarzania warstw na nadstopach niklu metodą CVD (Chemical Vapour Deposition). Oprogramowanie stanowić będzie podstawowe narzędzie w procesie projektowania i wytwarzania warstw metodą CVD. Opracowana technologia stanowić będzie ekonomiczną i techniczną alternatywę dla obecnie stosowanych metod określania warunków prowadzenia procesu wytwarzania warstw przy zachowaniu dobrych właściwości żaroodpornych. Podstawą oprogramowania są nowoczesne rozwiązania termodynamiki procesów nieodwracalnych (Linear Irreversible Thermodynamics) opracowanych w USA (H. Brenner, Faculty of Chemical Engineering MIT), Polsce (Danielewski i Wierzba AGH, Interdyscyplinarne Centrum Modelowania Materiałów oraz na Ukrainie (Gusak, Cherkassy State Univ.).
Unikatową cechą modelu procesów CVD i PCVD będzie zastosowanie po raz pierwszy w świecie modelu łączącego fenomenologiczny opis reakcji z termodynamiką procesów nieodwracalnych. Obok powszechnie używanego prawa zachowania masy, po raz pierwszy w termodynamicznych obliczeniach kinetyki reakcji połączone zostaną prawa ciągłości objętości i relacje Gibbsa-Duhema (pozwalające na określanie składu fazowego i prędkości wzrostu warstw) oraz równanie ruchu (pozwalające na określenie ewolucji i wpływu naprężeń).
Aspekt praktyczny opracowanych wyników badań w ramach realizowanego projektu: (1) obniżenie pracochłonności doboru warunków procesu do wytwarzania warstw aluminidkowych na nowych gatunkach nadstopów niklu oraz, łopatkach o różnych wymiarach, (2) podstawowe narzędzie do opracowania nowych technologii wytwarzania warstw żaroodpornych metodą CVD oraz prognozowania ich składu fazowego i właściwości, (3) podstawa do wdrożenia oprogramowania sterującego procesem nakładania powłok metodami CVD w celu uzyskania warstw o powtarzalnej budowie i właściwościach. Warstwy te będą spełniać wymagania konstruktorów, technologów oraz wysokie normy ekologiczne.

Lokalna prędkość dryftu w układzie AlCrNi na podstawie obliczeń procesu aluminiowania
Kierownik projektu: dr inż. Andrzej Nowotnik, Tel. +48 17 865 11 21, email: nowotnik@prz.edu.pl
Nowoczesne technologie materiałowe stosowane w przemyśle lotniczym
Projekt kluczowy No. POIG.01.01.02-00-015/08
Temat badawczy ZB nr 10: Nowoczesne pokrycia barierowe na krytyczne części silnika
Temat badawczy ZB nr 11: Materiały lotnicze o zaawansowanej strukturze (monokryształ, krystalizacja kierunkowa)
Współpraca z:
- Odlewnia Precyzyjna, WSK "PZL–Rzeszów" S.A.
Opis projektu:
Wykonanie badań do oceny doskonałości struktury krystalicznej rdzeniowanych odlewów monokrystalicznych z nadstopu niklu CMSX-4
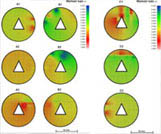
Opracowanie i wdrożenie technologii kształtowania plastycznego z nagrzewaniem oporowym elementów silników lotniczych z trudnoodkształcalnych nadstopów niklu i żelaza
Projekt realizowanego w ramach Programu „INNOTECH” w ścieżce programowej „IN-TECH”
Nr INNOTECH-K2/IN2/39/182334/NCBR/13
Współpraca z:
- WSK „PZL-Rzeszow” S.A.
Opis projektu:
Celem projektu jest opracowanie i wdrożenie technologii kształtowania plastycznego wybranych demonstratorów elementów podzespołów silników lotniczych wykonywanych z trudnoodkształcalnych blach nadstopów niklu i żelaza. Innowacyjnym rozwiązaniem w technologii jest zastosowanie nowatorskiej techniki elektrycznego nagrzewania oporowego wsadu – blachy. Nagrzewanie oporowe umożliwi skrócenie czasu operacji nagrzewania oraz przeniesienia wsadu do prasy. Oprzyrządowanie do nagrzewania oporowego będzie znajdować się bezpośrednio przy narzędziach kształtujących. Zaprojektowana i wykonana konstrukcja oprzyrządowania do nagrzewania oporowego oraz opracowana technologia kształtowania blach z jej zastosowaniem umożliwi obniżenie kosztów produkcji również poprzez zmniejszenie liczby operacji technologicznych. Osiągnięcie zamierzonego celu projektu wiążę się z realizacją zadań badawczych w zakresie opracowania: - modelu numerycznego procesu wytwarzania wybranych elementów z blach stopów trudnoodkształcalnych, - założeń konstrukcyjnych doświadczalnego stanowiska badawczego do nagrzewania oporowego i kształtowania plastycznego blach. Ponadto dla ustalenia kryteriów doboru warunków procesu kształtowania trudnoodkształcalnych blach nadstopów niklu i żelaza będą prowadzone badania: - mikrostruktury, właściwości mechanicznych i anizotropii lach badanych stopów (m.in. Inconel 625, Inconel 718, 17-4 PH, AISI 410) w temperaturze pokojowej i podwyższonej (do 500ºC), - wpływu warunków odkształcania plastycznego (temperatura, prędkość odkształcania) na wartość naprężenia uplastyczniającego, - wpływu rodzaju materiału i geometrii półwyrobu lub wyrobu oraz sposobu nagrzewania oporowego na rozkład wartości temperatury w kształtowanych plastycznie elementach podzespołów silnika.
Sterowanie frontem krystalizacji łopatek turbin niskiego ciśnienia z nadstopów niklu odlewanych w próżni poprzez zmianę cech geometrycznych formy ceramicznej, sposobu jej wyżarzania i ocieplania
Projekt nr U-8140/G/R
Współpraca z:
- Odlewnia Precyzyjna, WSK "PZL–Rzeszów" S.A.
- Wydział Odlewnictwa, AGH Kraków
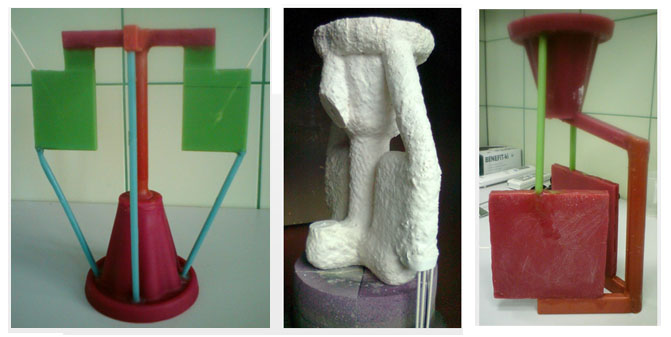
Zestaw modelowy woskowy (po lewej) i forma ceramiczna (w środku) do pomiaru współczynnika wymiany ciepła pomiędzy formą ceramiczną i odlewem. Po prawej zestaw modelowy woskowy z płytami o grubości 8.5 i 11.5 mm do pomiaru współczynnika zarodkowania objętościowego ziarn w odlewie, w zależności od przechłodzenia stopu.
Opracowanie i wdrożenie zintegrowanego systemu projektowania i technologii wytwarzania instalacji rurowych turbinowych silników lotniczych
Projekt badawczy celowy nr 6 ZR6 2007/C/07010 (2009-2011)
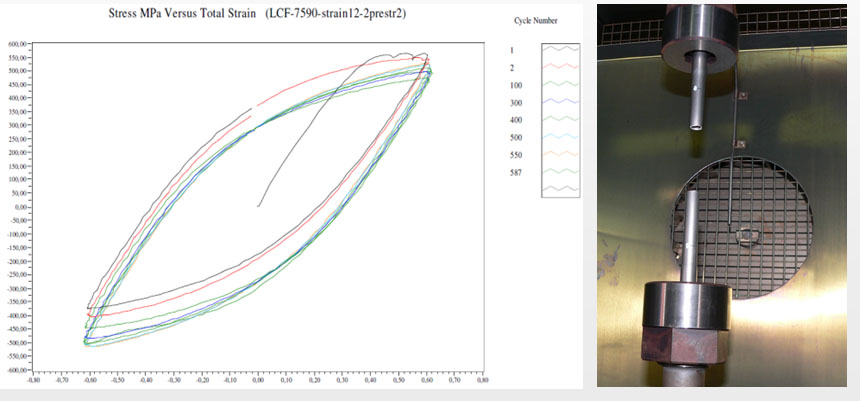
Próba statyczna rozciągania oraz próba zmęczeniowa w zakresie małej liczby cykli, w temperaturze pokojowej oraz podwyższonej, materiałów instalacji rurowej oraz próbek rurowych bez odkształcenia i z odkształceniem wstępnym